Advantages of Orbital Welding for High Purity Applications
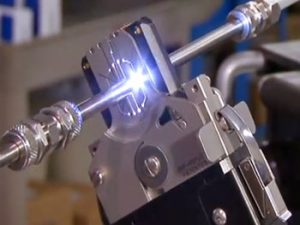
Orbital welding is a clean and highly effective way to join two objects together. The process involves moving the head around a stationary object. There are many advantages of orbital welding.
Orbital welding is ideal for a number of special situations including:
- When the tube or pipe cannot be rotated or rotation is not practical
- When space restrictions limit the size of the device that can be used
- In applications with strict requirements for quality, consistency and purity
Clean Welding
It’s important to keep contamination away from metal tubing during the welding process. Impurities can easily destroy an entire process, costing a significant amount of time and money. Orbital welding is extremely clean. It is generally performed in a clean room setting where tubes and fittings can be welded in a high-purity, contamination free environment.
High Quality Welding
An orbital weld performed using the right equipment and settings will always result in a high quality weld. This makes orbital welding the perfect choice for applications with strict requirements such as in the semiconductor and pharmaceutical industries.
Efficient Welding
Welds are always consistent and clean making the welding process extremely efficient. Computerized welding is even more efficient as the entire process can be scheduled ahead of time and documented. This reduces costs as well as production time.
Consistent Welds
With manual welding there will always be a level of variability and inconsistency between welds. Orbital welding produces consistent welds every time. This is due to the fact that orbital welding equipment can be set to a specific program, allowing the system to repeat the exact same welds time and time again.
Means Engineering, Inc. has the capabilities and equipment necessary to perform high purity welding services for a wide range of industries. Our highly skilled employees offer high quality orbital welding to semi E-49.